ROCKET STATIC TEST STAND

Building your own rocket motors is all very well, but without a good thrust curve, and any meaningful data, ultimately, it's a bit pointless.
Hence the need for a static test stand.
Because the main focus of my rocketry is based around hybrid rocket motors, I figured I needed a static test stand which I could use with hybrids. Initially, my plan was to build a small static test stand for microhybrid sized rockets, and slightly larger hybrids up to 38mm diameter, then I thought maybe I should build something a bit larger to cater for a wider variety of rocket motors.
The design I settled on, borrows heavily on the excellent Test Stand 2 designed by Bob Fortune of Aerocon. Bob Fortune is extremely knowledgeable on all things rocket related, so I figured his design must be pretty good. Added to that he is a thoroughly decent chap, who I have bought a number of rocket components off in the past.
So, taking the design of Bob Fortune's test stand as a baseline, I went away and did a bunch of calculations to work out what the most appropriate materials and dimensions of a static test stand would be for various thrust loadings. I remember not paying much attention for those lectures in my Physics degree, but luckily, even many years later, I found I still had some useful books which I was able to refer to for the calculations and materials details.
My problem was, I could forsee a need for both a horizontal static test stand, and a vertical static test stand. Bob Fortune's design seemed to cater for both configurations, so it made perfect sense to use this design.
Next on my list was to phone my mate Danny to run the idea past him, and to see if I could borrow his metal workshop. As an ex Glaswegian welder who has welded anything from Oil Rigs to steel furniture, his input would be invaluable. An hour and a half phonecall later, I was happy, I had a date fixed up to use his workshop, and it would only cost me a modest amount of alcohol. All I had to do now, was order the components.
CONSTRUCTION.
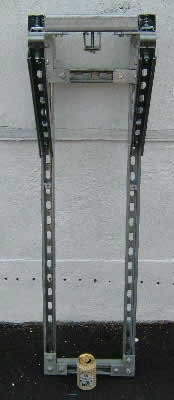
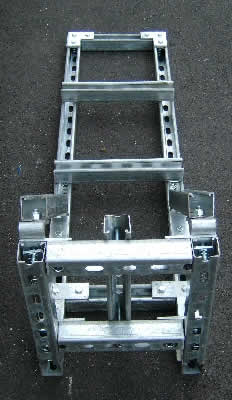
The static test stand is constructed from heavy duty, galvanised steel Unistrut (41mm x 41mm cross section), with a 1100mm long bed, with 2 rails separated by 300mm wide crosspieces, and all bolted together with M8 nuts and bolts. It disappointed my welder friend Danny that he didn't need to do any welding, but he thought the Unistrut would be a better solution in this case anyway.
The use of Unistrut enables the static test stand to be bolted down to whatever solid surface is to be used for the static tests. The Unistrut based test stand has the advantage that it is very heavy, which is what you really want for a static test stand, but it also has the disadvantage in that galvanised steel is a real pain to work with, really difficult to drill and cut through.
INSTRUMENTATION.
There are 2 boxes attached to the static test stand (not shown here), the first houses the sensor system. This is designed to provide a robust housing to accomodate thermocouples, pressure sensors, an acoustic sensor, and a vibration sensor.
The sensors are connected via a cable, to an Amplifer and a Data Acquisition System. The Data Acquisition System is connected via an RS-232 connection to the serial port of the laptop computer, where the data is fed into the data logging system.
MONITORING.
Because the static test stand is obviously operated remotely, a high resolution CCD colour bulletcam is also mounted on the static test stand to enable static tests to be viewed close up by the remote operator.
CONTROL.
The second box houses a simple wiring circuit for the ignition system, and provides a way of neatly plugging a cable from a launch/firing controller in, along with a large 12 volt battery, and then providing outputs to the igniter.
TIPS.
- Don't forget to ensure that your calculations make the static test stand able to take considerably greater motor thrusts than the maximum thrust motor you intend to use. Good Safety Factors really are essential on a project such as this.
- Don't forget to bolt any static test stand you build or use to an immovable object of greater mass than the thrust of the rocket motor you are testing.
ACKNOWLEDGEMENTS.
Bob Fortune of Aerocon is owed a big debt of thanks for providing the inspiration for my rocket static test stand design. His website is an absolute goldmine of fascinating information and equipment to buy. My mate Danny is long suffering of my pestering to use his workshop for my various rocketry ideas, and he does provide very good feedback from a practical "been there, built it" perspective, and I am very grateful to him for all his help.
See Also
Hybrid Rocket Science, Hybrid Rocket Help Clinic, Amateur Hybrid Motors, Amateur Liquid Rockets, Guidance, Gimballed Motors, Launch Controller, UK Rocketry Vendors, UK Rocket Groups, UK Space Organisations